As a brewer, you want to make sure your customers get the optimum experience when they order your beer in a bar.
As the brewing industry continues its journey toward greener practices, the spotlight is increasingly on smarter logistics and sustainable packaging.
At Duotank, we understand the urgency for breweries to reduce their environmental footprint—without compromising on quality or efficiency. One innovation that’s making a meaningful difference? Tankbeer systems.
In this blog, we explore how tankbeer offers a more sustainable approach across production, transportation, usage, and cleaning—helping breweries move toward a more eco-conscious future.
Sustainable Production: Reusable Tanks, Recyclable Materials
Tankbeer systems significantly lower their environmental impact compared to traditional beer logistics. The tanks are made of high-grade stainless steel, a durable material that can be reused for decades and is almost entirely recyclable—often already containing recycled content when produced.
The only single-use component in the system is the inliner—a food-grade plastic bag that holds the beer inside the tank. While once considered a weak point in terms of sustainability, today’s inliners are increasingly made from fully recyclable materials, marking a big step forward in reducing waste and enhancing the system’s eco-friendliness.
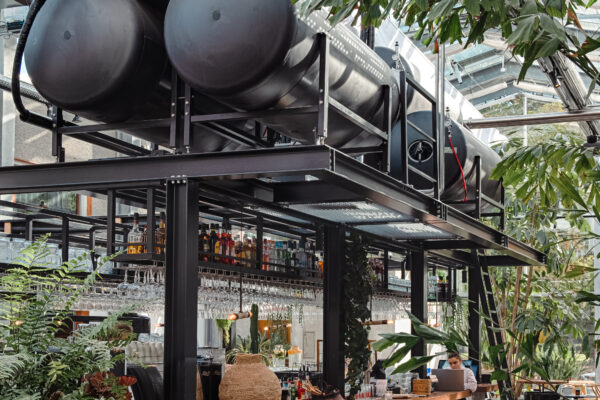
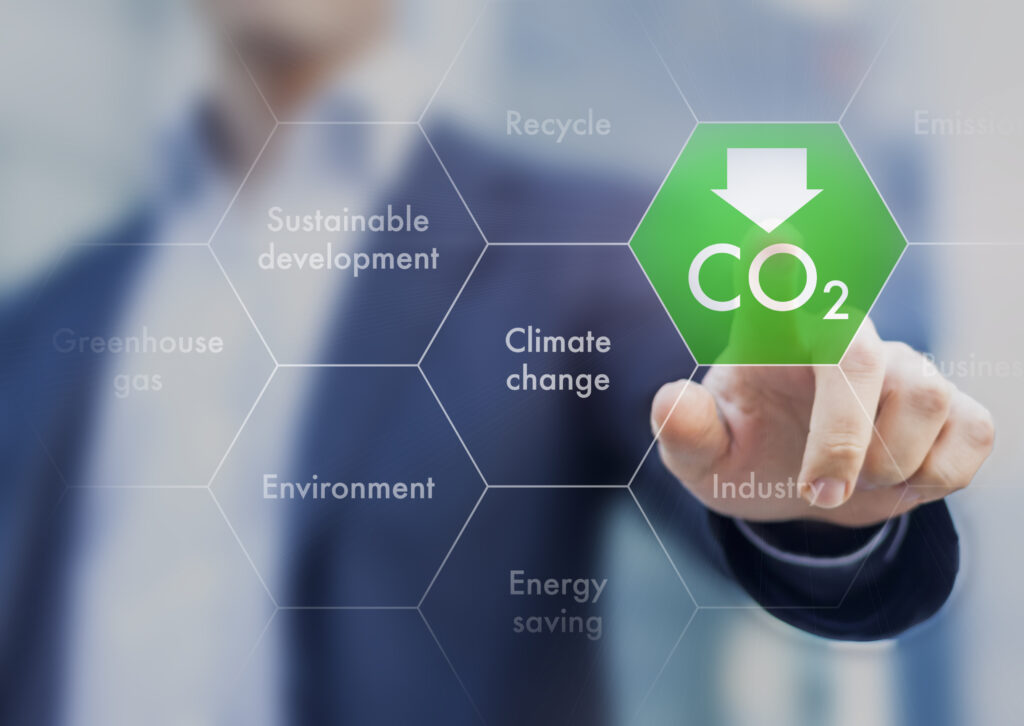
Smarter Logistics: No Empty Returns, Less Fuel Use
When it comes to transport, tankbeer also shines. Unlike kegs, there’s no need to return empties—reducing round-trip shipping. As the tank empties during delivery, the total vehicle weight decreases, cutting down fuel consumption and emissions throughout the delivery cycle. It’s a win for efficiency and the environment.
Eco-Friendly in Use: Less CO₂, No Wastewater
Perhaps the biggest sustainability win is seen during the usage phase. Traditional keg systems rely on CO₂ to push beer out of the container, but tankbeer systems use compressed air instead.
Let’s compare:
- Tapping 50L of beer from a keg uses approximately 6 kg of CO₂.
- Tapping the same amount from a tankbeer system uses only 3 kg of CO₂, through compressed air production.
That’s a staggering difference in carbon emissions.
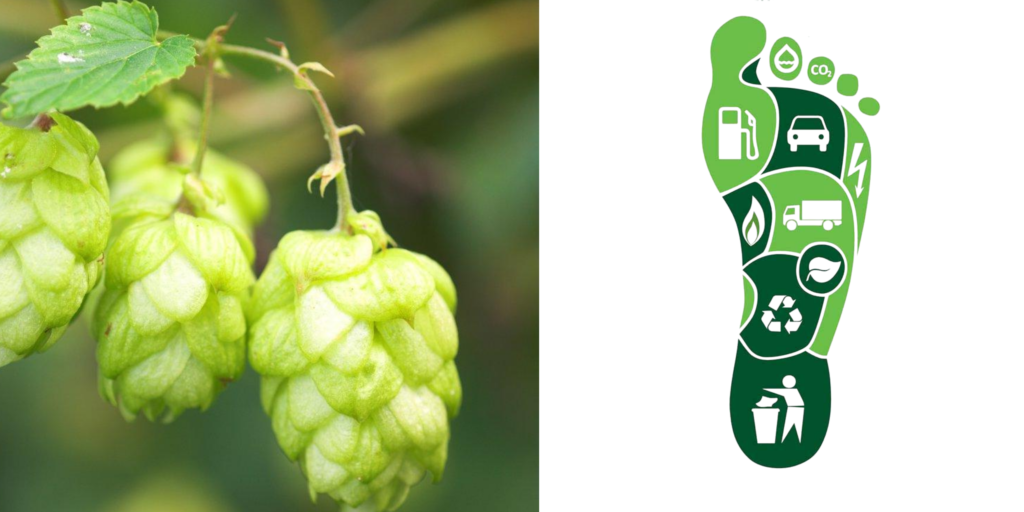
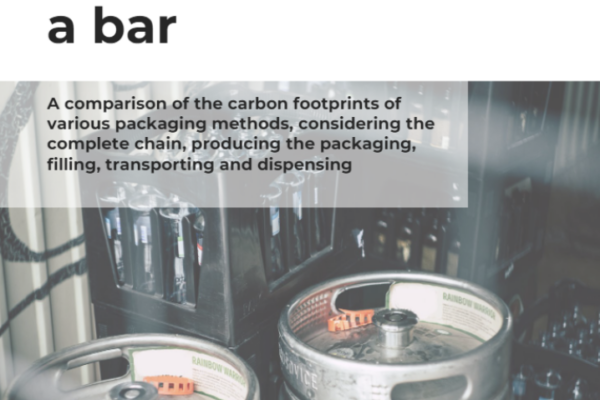
Easy, Water-Free Cleaning
Once the tank is empty, there’s no need for a deep clean. The process is as simple as removing the used inliner and replacing it with a new one. This eliminates the need for water, chemicals, and energy-intensive cleaning cycles—a major contrast to the extensive cleaning required for reusable kegs and bottles.
The Bottom Line: Better Beer, Lower Footprint
Tankbeer systems offer breweries a smarter, cleaner, and greener way to distribute their product. From production to pour, the environmental benefits are clear—and growing with every innovation.
Want to dive deeper?
Download our whitepaper for a full comparison between tankbeer and traditional distribution methods.
Recent articles
Combined Tankbeer Transport: Efficiency, Sustainability and Innovation in One
As a brewer, you want to make sure your customers get the optimum experience when they order your beer in a bar.
Blog: comparing single-wall and double-wall beer tanks
As a brewer, you want to make sure your customers get the optimum experience when they order your beer in a bar.
Blog: Filling your beer tank; the do’s and don’ts
As a brewer, you want to make sure your customers get the optimum experience when they order your beer in a bar.
Blog: your first tankbeer installation and how Duotank will help you
As a brewer, you want to make sure your customers get the optimum experience when they order your beer in a bar.
Blog: tankbeer systems for stadiums and concert halls
As a brewer, you want to make sure your customers get the optimum experience when they order your beer in a bar.
Blog: understanding how a tankbeer systems keeps beer at the right temperature
As a brewer, you want to make sure your customers get the optimum experience when they order your beer in a bar.
Blog: Tankbeer transport: finding the right set-up for your unique situation
As a brewer, you want to make sure your customers get the optimum experience when they order your beer in a bar.
Blog: a deep dive into the Pressure Equipment Directive (PED)
As a brewer, you want to make sure your customers get the optimum experience when they order your beer in a bar.
Blog: Using compressed air instead CO2
As a brewer, you want to make sure your customers get the optimum experience when they order your beer in a bar.